文章信息
- 王伟超, 刘希亮, 苏承东
- WANG Weichao, LIU Xiliang, SU Chengdong
- 盐岩巴西劈裂疲劳变形和强度特性研究
- Study of deformation and strength characteristics of Brazilian splitting fatigue tests of salt rock
- 武汉大学学报(工学版), 2018, 51(4): 305-313
- Engineering Journal of Wuhan University, 2018, 51(4): 305-313
- http://dx.doi.org/10.14188/j.1671-8844.2018-04-005
-
文章历史
- 收稿日期: 2016-10-06
2. 河南理工大学河南省高等学校深部矿井建设重点学科开放实验室,河南 焦作 454003;
3. 河南理工大学能源科学与工程学院,河南 焦作 454003
2. Henan Colleges and Universities Deep Mine Construction Key Discipline Open Laboratory, Henan Polytechnic University, Jiaozuo 454003, China;
3. School of Energy Science and Engineering, Henan Polytechnic University, Jiaozuo 454003, China
岩土工程经常会受到周期性荷载作用,围岩在周期性荷载作用下的力学特性是影响岩土工程疲劳寿命的重要因素之一.因此,岩石的疲劳破坏机制对岩体的长期稳定性和安全性具有重要意义,受到国内外学者的广泛关注.
国内外学者[1-6]对于岩石(类岩石)材料开展大量疲劳破坏试验,研究发现岩石的疲劳寿命与上限应力比、加载波形、应力幅值有关.冯春林等[1]对白砂岩在周期荷载作用下的疲劳破坏过程进行研究表明,上限应力和振幅是影响疲劳破坏过程的主要因素,应变速率与疲劳寿命呈负相关性,并且按照指数曲线发展.朱晶晶等[2]利用改进的大直径霍布金森杆体(SHPB)试验系统,对花岗岩进行单轴循环冲击压缩试验,分析其在循环冲击载荷下的力学特性及能量吸收规律.苏承东等[3]对砂岩进行劈裂疲劳破坏试验,研究结果表明疲劳上限载荷(应力)比、抗拉疲劳强度与循环次数呈负相关.Erarslan等[4]对预制裂纹的类岩石材料进行劈裂试验研究,分析其疲劳损伤的断裂模式.
盐岩以其低渗透性、损伤后能自我恢复的优点[7],可作为石油和天然气等战略能源的地下储存介质.目前,我国正在逐步加大盐穴地下能源储库建设,国内学者也开展了大量的研究工作.郭印同等[8]试验研究了单轴循环荷载下盐岩的疲劳强度、变形及损伤特性,盐岩的循环疲劳破坏过程同样受到静态全过程曲线的控制.杨春和等[9]在盐岩单轴循环加卸载试验中发现,随着荷载级别的增高,无论是卸载还是再加载,直线段的变形模量总体上呈上升的趋势.马林建等[10]认为通过试验可间接推断盐岩三轴循环变形破坏的上限应力阈值为80%~89%,并发现盐岩2次压缩表现出比1次压缩更为显著的应变硬化特征.
盐穴储库在运营过程中,受注采周期荷载影响,围岩应力场不断发生变化.然而,上述学者的研究大多关注于盐岩的单、三轴压缩疲劳破坏,缺乏对于盐岩受拉压循环载荷作用下的变形和强度特征研究.当然,在工程实践中,岩体大多处于二向或三向应力状态,很少有单向拉破坏,但很多破坏都初始于局部受拉破坏.从试验方法上看,文献[3]仅采用恒频率、恒幅值、恒定平均荷载的循环荷载对砂岩受拉疲劳特性进行研究.为分析盐岩的抗拉疲劳强度与变形特征,本文分别采用恒频率、恒幅值下的正弦波,进行常规巴西劈裂试验,同时,分别采用恒幅值、恒定平均荷载的循环荷载进行恒定平均荷载劈裂疲劳试验(本文简称为恒荷载疲劳法),采用恒幅值、变化平均荷载的循环荷载进行变平均荷载劈裂疲劳试验(本文简称为变荷载疲劳法),以期为工程实践提供借鉴和参考.
1 试验方法为减小试验结果的离散度,本试验采用宏观较均匀、颜色一致、结构致密的高纯度喜马拉雅盐岩.试件加工过程中,由于盐岩较软,并且易溶于水,采用直径为50 mm取芯钻取芯,然后用干式锯磨法进行试件的切割加工,将盐岩试件加工成圆柱体,劈裂法试验的厚径比为0.5~1.0,端面平行度为±0.02 mm,满足测定方法的要求,岩样具体尺寸见表 1.
分组 | 编号 | 试验方法 | D /mm |
L /mm |
P /kN |
Rt/MPa |
第1组 | BJA-1 | 平板劈裂 | 50.60 | 40.70 | 6.412 | 2.004 |
BJA-2 | 平板劈裂 | 50.32 | 42.16 | 6.642 | 1.993 | |
BJA-3 | 平板劈裂 | 50.80 | 40.38 | 6.602 | 2.049 | |
BJA-4 | 平板劈裂 | 50.62 | 44.80 | 7.340 | 2.061 | |
BJA-5 | 平板劈裂 | 50.78 | 46.00 | 7.102 | 1.939 | |
平均 | 6.820 | 2.009 | ||||
第2组 | BJC-4 | 钢丝劈裂 | 50.60 | 40.20 | 5.716 | 1.789 |
BJD-1 | 钢丝劈裂 | 50.40 | 44.90 | 5.096 | 1.434 | |
BJE-1 | 钢丝劈裂 | 50.52 | 45.90 | 6.072 | 1.667 | |
BJF-1 | 钢丝劈裂 | 50.30 | 44.20 | 4.286 | 1.227 | |
BJF-2 | 钢丝劈裂 | 50.70 | 43.24 | 6.452 | 1.874 | |
*BJH-1 | 钢丝劈裂 | 50.70 | 45.70 | 3.712 | 1.020 | |
BJH-2 | 钢丝劈裂 | 50.80 | 47.00 | 6.758 | 1.802 | |
平均 | 5.73 | 1.632 | ||||
*:结果离散,未参与计算. |
试验设备采用中国科学院武汉岩土所研制的RMT-150B岩石力学试验系统,该系统可进行不同波形、不同频率和不同幅值的疲劳试验.由于不同的加压方式造成测定的岩石抗拉强度差别很大[11],为准确测定盐岩的抗拉强度,首先进行常规劈裂试验,并采用2种加压方式:一种为钢丝垫条加载劈裂法,称为钢丝劈裂法,钢丝直径为2 mm,示意图见图 1(a);另一种使用钢性垫块直接加载,称为平板劈裂法.垂直方向(用y表示)和水平方向(用x表示)布置传感器分别测量压缩和拉伸变形量.其次,进行恒荷载疲劳和变荷载疲劳试验,根据常规劈裂试验结果,设置劈裂疲劳试验参数,疲劳荷载波形示意图如图 2所示,图中的上限、下限和平均荷载分别用Pmax、Pmin和P0表示,幅值(波峰与波谷差值)ΔP=Pmax-Pmin.
![]() |
图 1 巴西劈裂试验加载图 Figure 1 Sketch map of Brazilian split test |
![]() |
图 2 巴西劈裂疲劳荷载波形示意图 Figure 2 Waveform of Brazilian split fatigue load |
按照图 1的加载方式,根据国家标准[12]常规劈裂试验试件的抗拉强度可表示为

式中:Rt为岩石抗拉强度;L为试件厚度;D试件为直径;P为试件破坏载荷.
2 常规劈裂试验 2.1 试验结果分析为合理设置疲劳试验参数,首先进行盐岩的常规劈裂试验,试验的实际加载情况见图 1(b),加载速率为0.05 kN/s.盐岩常规劈裂试验结果见表 1,表中:P为常规劈裂破坏荷载; Rt为劈裂试验试件的抗拉强度.从表中可以看出:第1组5个试件劈裂试验破坏荷载为6.412~7.34 kN,平均值为6.82 kN.依据公式(1)可得到抗拉强度为1.939~2.061 MPa,平均值为2.009 MPa.而第2组7个试件中,尽管试件宏观均匀、颜色一致,但试验结果仍存在一定离散性,由于试件BJH-1破坏荷载和抗拉强度最低,离散较大,未参与平均值计算,劈裂破坏荷载为4.286~6.758 kN,平均值为5.73 kN,抗拉强度为1.227~1.802 MPa,平均值为1.632 MPa.下文尝试从盐岩巴西劈裂破坏断口形貌角度对离散原因进行分析.对比2组试验数据,第1组比第2组平均值高出23.1%,钢丝劈裂法试验结果普遍小于直接加载的试验结果,钢丝劈裂法结果平均值明显小于平板劈裂法结果平均值,经下文对结果的理论分析后,在劈裂疲劳试验中,本文采用钢丝加载方式进行.
图 3为盐岩试件钢丝劈裂法下垂直变形-时间、荷载-变形曲线.图中:垂直方向的压缩变形为正值,用y来表示;水平方向的拉伸变形为负值,用x来表示.从图 3(a)可以看出,常规劈裂破坏的变形特征与砂岩劈裂破坏相类似,分为压密、弹性、屈服和破坏4个阶段[3].压密阶段主要表现为曲线的起始位置有略微的上凹现象,其原因主要2个:1)试件本身存在缺陷(空隙和裂纹)的压密过程,尤其试件与钢丝垫条接触处更加明显;2)试件表面不够光滑,与钢丝接触处发生局部变形.弹性阶段主要表现在随着荷载的增大,变形量呈线性增加,表现出弹性特征.屈服阶段主要表现在曲线在接近峰值处不再呈现线性特征,而呈现略微的上凸现象.破坏阶段当荷载达到极限承载力时,突然破坏,时间很短,但仍然有一定的变形量,这一特征与砂岩的破坏阶段明显不同[3],其原因可能在于盐岩较软,在加载点存在应力集中,在试件拉断前出现了钢丝切入情况所致.其中,试件BJF-2曲线初始阶段上凹比较大,可能是试件表面过于粗糙所致;而试件BJD-1出现的明显上凸现象则可能在初始加压时,传感器与垫板之间发生了相对移动,与造成的测量误差有关.由图 3(b)也可看出经历的4个阶段.经过压密阶段后,随着加载时间的增加,垂直变形基本呈线性增加,在屈服阶段时,垂直变形逐渐加大,达到破坏荷载,试件突然断裂而垂直变形猛然增加.
![]() |
图 3 钢丝劈裂法试验曲线 Figure 3 Curve of wire split tests |
利用巴西圆盘劈裂试验间接获得岩石类材料抗拉强度的方法是国际岩石力学学会(ISRM)推荐采用的,其理论基础是对称的线荷载作用下圆盘力学问题可以简化为平面应变问题[13].如图 4(a)所示的直径为D的圆盘,受到大小为p(p=P/L)的集中荷载,圆盘内一点M(x,y)的受力状态:
![]() |
图 4 试件受力示意图 Figure 4 Sketch map of Brazilian disk test |



式中:D为圆盘直径;L为圆盘厚度;P为破坏荷载.当点M位于荷载右侧时θ1、θ2为正,位于左侧时为负.
在试件圆心O处,θ1=θ2=0,r1=r2=D/2,代入式(2)、(3),可得圆心处拉压应力分别为

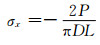
可见,圆心处压应力为拉应力的3倍,由于岩石类材料的抗压强度远高于抗拉强度,故此处受拉应力主导而开裂.实际试验加载过程中,在采用钢丝劈裂法时,尽管存在误差,合金钢丝仍可近似认为传递线荷载,计算结果可按式(6)计算.当采用平板劈裂法时,由于盐岩较软,强度相对花岗岩等硬岩强度较低,加载过程中,试件与加载平板接触处,产生塑性变形,荷载由线荷载传递逐渐过渡为面荷载传递[14],此时圆盘的受力便不再是图 4(a)所示的垂直方向的点荷载作用,而成为图 4(b)所示的线荷载作用,线荷载长度a与平台角2α相关.因此,破坏时的作用荷载:

此时,再利用式(1)计算抗拉强度必然带来较大的误差,从而造成第1组比第2组的抗拉强度平均值高出23.1%的现象.文献[15]对岩石开展平台圆盘劈裂试验,研究不同的平台中心角对抗拉强度的影响.
3 巴西劈裂疲劳试验 3.1 试验结果分析 3.1.1 恒荷载疲劳试验结合上文分析,以钢丝劈裂法开展劈裂疲劳试验.为厘清盐岩巴西劈裂疲劳全过程的变形和破坏特征,首先开展恒荷载疲劳试验.根据常规劈裂试验结果,确定劈裂疲劳试验的平均荷载水平为3.4 kN,上限载荷为4.86 kN,上限载荷(应力)比约为0.85,下限载荷为1.79 kN,下限载荷(应力)比约为0.31.为避免疲劳试验的变形-荷载曲线太过密集,采集系统设定当变形量超过0.012 5 mm时记录1个滞回环.
从试验结果来看,盐岩劈裂疲劳寿命离散性较大,但从变形发展和塑性变形累积演化来看,也具有明显的阶段性特征.下面以试件BJF-3为例进行分析,图 5给出了试件BJF-3的劈裂疲劳全过程荷载-垂直变形及荷载-水平变形曲线.
![]() |
图 5 恒荷载疲劳法荷载-变形曲线 Figure 5 Load-deformation curves of Brazilian split fatigue tests of constant average load |
从图 5可以看出,荷载-垂直变形曲线分2个部分:第1部分OA段为静力加载阶段,荷载以速率为0.05 kN/s的力控制形式匀速加载,加载至平均荷载水平停止,荷载与变形成线性关系;第2部分AB段为劈裂疲劳阶段,循环荷载从平均荷载值开始加载,以1 Hz频率的正弦波加载,直到试件破坏.AB段曲线呈现出明显的疏—密—疏3个阶段性特征.第1阶段是循环开始阶段,轴向变形发展较快,每个循环都有较明显的变形,该阶段累积了较大变形;短期循环后,随着循环增加,变形速率逐步趋于稳定,即进入变形以等速率发展的第2阶段,该阶段应变发展速率较稳定,轴向应变发展很慢,占疲劳寿命的大部分;进入第3阶段,在循环的最后阶段,随着循环次数的增加,试件变形速率急剧增大,试件也快速突然破坏,该阶段经历时间很短,循环次数也很少.此曲线特征与白砂岩[1]和红砂岩[16]循环压缩的曲线特征有相似之处,支持了疲劳破坏曲线呈现的疏—密—疏3个阶段性特征,表明试验结果合理可靠.从破坏机理上说,试件在循环荷载作用下,每次的加卸载循环都产生弹性和塑性变形,塑性变形是由于试件内部应力变化损伤造成的,曲线上则表现为滞回环.随着循环次数的增加,滞回环累积的塑性变形逐步加大,即岩样的不可逆变形逐步发展而致试件快速破坏.
从图 5不难看出,荷载-水平变形曲线与垂直变形曲线相似,也呈现明显的疏—密—疏3个阶段性特征,此特征与红砂岩[16]的变形特征明显不同.根据图 6的曲线原始数据,计算每个滞回产生的变形量,绘出其随循环次数变化的散点图如图 6所示.可以看出,整个疲劳过程的变形可以划分为3个阶段.
![]() |
图 6 滞回环数与变形关系 Figure 6 Relationship between hysteresis loop and deformation |
变荷载疲劳法试验过程中,保持循环荷载幅值不变,初始平均荷载水平P1时,开始循环加载500次,为进行对比分析,BJF-4加载3 100次.然后增加平均荷载0.5 kN,再加载500次循环荷载,随后每加载500次循环荷载,增加一个荷载水平,直到试件完全破坏.表 2给出盐岩试件变荷载疲劳法试验结果.
编号 | 尺寸 /(mm×mm) |
P1 /kN |
荷载级数 | Pmax /kN |
N | M /mm |
BJB-4 | 50.7×44.9 | 3.0 | 4 | 5.9 | 1 502 | 0.93 |
BJD-2 | 50.6×42.3 | 3.0 | 4 | 6.1 | 2 000 | 0.69 |
BJD-5 | 50.6×43.4 | 3.0 | 6 | 7.1 | 2 590 | 0.95 |
BJH-4 | 50.9×46.6 | 2.6 | 4 | 6.5 | 2 000 | 1.15 |
BJF-4 | 50.1×44.4 | 3.4 | 5 | 7.0 | 5 198 | 0.95 |
*:E-3 | 50.7×37.5 | 3.0 | 1 | 3.7 | 0 | |
*:E-4 | 50.6×41.1 | 3.0 | 1 | 3.1 | 0 | |
*:试件强度离散,循环试验失败,不参与计算. |
表 2中,P1为第1级平均荷载值;Pmax为试验破坏前一个完整周期循环中的最大荷载值;N为周期循环加载总次数;M为试件破坏时垂直方向的总变形量.
从表 2中可以看出:每个试件荷载循环加载总次数N有比较大的离散性,从试验疲劳破坏荷载Pmax来看,平均值为6.52 kN,变形量平均值为0.93 mm,但每500个循环的滞回环数和变形量有较明显的规律可循.为更准确地分析,表 3给出加载过程中每级荷载值、滞回环数和变形量,表中Pi(i=1~6)为第i级平均荷载,T0为第1级荷载水平加卸载循环次数,Ni(i=1~6)为第i级加载时形成的滞回环数,Mi(i=1~6)为第i级加载时产生的垂直变形量.试件BJF-4在第1个荷载水平加、卸载3 000次,为便于比较研究,表 3最后一行给出第1荷载水平每500次产生的滞回环数和变形量.
编号 | P1 /kN |
幅值 /kN |
T0 | M1 /mm |
N1 | P2 /kN |
M2 /mm |
N2 | P3 /kN |
M3 /mm |
N3 | P4 /kN |
M4 /mm |
N4 | P5 /kN |
M5 /mm |
N5 | P6 /kN |
M6 /mm |
N6 |
BJB-4 | 3.0 | 3 | 500 | 0.32 | 58 | 3.5 | 0.12 | 31 | 4.0 | 0.16 | 43 | 4.5 | 0.07 | 2 | ||||||
BJD2 | 3.0 | 3 | 500 | 0.23 | 44 | 3.5 | 0.08 | 20 | 4.0 | 0.09 | 21 | 4.5 | 0.11 | 30 | ||||||
BJD-5 | 3.0 | 3 | 500 | 0.24 | 45 | 3.5 | 0.06 | 23 | 4.0 | 0.09 | 24 | 4.5 | 0.11 | 27 | 5.0 | 0.11 | 30 | 5.5 | 0.04 | 14 |
BJH-4 | 2.6 | 3 | 500 | 0.29 | 53 | 3.4 | 0.10 | 28 | 4.0 | 0.11 | 30 | 4.5 | 0.14 | 40 | ||||||
BJF-4 | 3.4 | 2.85 | 3 000 | 0.37 | 78 | 4.0 | 0.07 | 17 | 4.5 | 0.08 | 22 | 5.0 | 0.11 | 29 | 5.5 | 0.15 | 44 | |||
BJF-4 | 3.4 | 2.85 | 500 | 0.29 | 53 | 3.4 | 0.02 | 4 | 3.4 | 0.02 | 4 | 3.4 | 0.02 | 4 | 3.4 | 0.02 | 4 | 3.4 | 0.02 | 4 |
图 7分别给出平均荷载水平与变形量和滞回环数的关系,从图中可以看出,在第1级平均荷载时,因处于刚开始“疏”的阶段,变形量和滞回环数量都较大,从第2级平均荷载开始,变形量、滞回环数与平均荷载水平都呈现近似线性增长.图 8为试件BJD-2变荷载疲劳法试验的荷载-垂直变形曲线图.结合表 3可以看出,在第1级荷载水平,循环荷载加载500次,曲线经过“疏—密—疏”3阶段的第1阶段,产生了较大的变形量,提高一级平均荷载水平后,加载500次循环荷载,变形量小于第1级,正是经历“密”的阶段(第2阶段),因此,尽管平均荷载稍大于前一级,但变形量小于第1级.随着荷载水平的逐步加大,每一级的变形量逐步增大.在破坏前的最后一级荷载水平时,在循环荷载作用过程中,变形量快速增加,试件随着变形的快速增加,突然破坏.
![]() |
图 7 变形随平均荷载水平的发展规律 Figure 7 Deformation law along with average load |
![]() |
图 8 变荷载疲劳法荷载-变形曲线 Figure 8 Load-deformation curves of Brazilian split fatigue tests of variational average loads |
为比较常规劈裂与劈裂疲劳试验过程中试件的强度与变形特征,将常规劈裂试件BJH-2和劈裂疲劳试件BJB-4同时绘出,如图 9所示,从图 9中可以看出,在劈裂疲劳破坏前的最大荷载值相较常规劈裂破坏荷载值有所降低.但是,总的来说,常规劈裂破坏荷载平均值为5.73 kN,而疲劳破坏荷载Pmax平均值为6.52 kN,疲劳破坏荷载均值不但没降低还稍微增加.从变形量上来看,试件BJB-4疲劳破坏时的总变形量不仅没有受到常规劈裂变形量的控制,还明显大于常规劈裂试件BJH-2破坏时的变形量.对于其他疲劳破坏试件,仅有BJD-2总变形量小于BJH-2,因此,对于盐岩的巴西劈裂疲劳破坏不会受到常规劈裂全过程曲线的控制,此变形特征不同于砂岩[3]的劈裂疲劳破坏.
![]() |
图 9 变荷载疲劳法与常规劈裂对比 Figure 9 Comparison between conventional split and split fatigue test with variational loads |
从宏观角度看,钢丝劈裂法的劈裂试件在加载基线处有明显的加载压痕,大多数试件都沿着钢丝加载条的加载基线断裂为2个对称的半圆,断口没有出现摩擦痕迹,呈现出拉破坏的脆性破坏特征.本文给出具有代表性的试件BJH-1和试件BJD-5的断口照片,如图 10所示.为更清楚盐岩断口形态与抗拉强度的关系,对试验后的盐岩试件劈裂破坏断口进行电镜扫描,得到30余幅不同倍数下的放大照片.
![]() |
图 10 试件破坏断口形貌 Figure 10 Fracture morphology of salt rock specimens |
从图 10中可以看出,尽管从外观看试件颜色一致,质地均匀,但由于盐岩在成岩过程中,受到压实作用、压溶作用、胶结作用和溶蚀作用等,形成粗晶、中晶、细晶盐岩或混合晶体盐岩.尽管微裂纹、夹杂含量等因素都影响盐岩的抗拉强度,但盐岩的结晶情况也是不可忽视的影响因素.
从微观角度看,岩石的微观断裂形式主要有穿晶断裂和沿晶断裂.从微观断口的形貌上又可分为解理断裂、沿晶断裂、微孔聚合断裂及任两者的耦合.岩石类材料拉断裂微观包括河流状花样、台阶状花样、舌状花样、鱼骨状花样、根状花样、等轴微坑及三角微坑状花样、晶界断裂花样、晶界及晶间断裂花样、晶间断裂花样9种[17].对图 10所示区域电镜扫描后见图 11,可以看出,试件BJD-5断口扫描区域,在断口表面呈自相似的随机晶界断裂花样,接触面积较大,更多呈沿晶断裂特征;观察此试件其他断口形貌,同时伴有少量穿晶断裂的耦合.试件BJH-1断口扫描区域,在断裂表面形成不规则的台阶状,断口两面接触面积很小,呈现明显的穿晶断裂特征;观察此试件其他断口形貌,同时伴随少量沿晶断裂的耦合.
![]() |
图 11 两试件断口SEM图像对比 Figure 11 Comparison of SEM images between specimens BJD-5 and BJH-1 |
1) 变荷载疲劳法荷载-变形曲线不受常规劈裂过程曲线控制,破坏时的变形量甚至大于常规劈裂试验的变形量.
2) 变荷载疲劳法试验中,在第1级平均荷载时,因处于刚开始“疏”的阶段,变形量和滞回环数量都较大,从第2级平均荷载开始,变形量、滞回环数与平均荷载水平都呈现近似线性增长.
3) 恒定平均荷载的劈裂疲劳破坏荷载-垂直变形曲线包括“疏—密—疏”3个阶段,分别为循环开始阶段、变形稳定发展阶段、变形加速阶段.与红砂岩明显不同,荷载-水平变形曲线也包括“疏—密—疏”3个阶段.
4) 对于盐岩等较软岩或软岩,开展劈裂试验时,由于直接加载过程中引起试件的压缩变形较大,破坏时类似平台圆盘劈裂破坏,采用常规数据处理方法造成结果偏差较大;采用钢丝劈裂法开展劈裂试验,采用常规数据方法处理后结果相对更准确.
5) 常规劈裂试验的变形特征与单轴压缩基本相似,分为压密、弹性、屈服和破坏4个阶段.
[1] |
冯春林, 吴献强, 丁德馨, 等. 周期荷载作用下白砂岩的疲劳特性研究[J].
岩石力学与工程学报, 2009, 28(增1): 2749–2754.
Feng Chunlin, Wu Xianqiang, Ding Dexin, et al. Investigation on fatigue characteristics of white sandstone under cyclic loading[J]. Chinese Journal of Rock Mechanics and Engineering, 2009, 28(Supp.1): 2749–2754. |
[2] |
朱晶晶, 李夕兵, 宫凤强, 等. 单轴循环冲击下岩石的动力学特性及其损伤模型研究[J].
岩土工程学报, 2010, 32(5): 657–662.
Zhu Jingjing, Li Xibing, Gong Fengqiang, et al. Experimental study of dynamic characteristics and damage model for rock under cyclical impact compressive loads[J]. Chinese Journal of Geotechnical Engineering, 2010, 32(5): 657–662. |
[3] |
苏承东, 张盛, 唐旭. 砂岩巴西劈裂疲劳破坏过程中变形与强度特征的试验研究[J].
岩石力学与工程学报, 2013, 32(1): 41–48.
Su Chengdong, Zhang Sheng, Tang Xu. Experimental research on deformation and strength characteristics in process of Brazilian split fatigue failure of sandstone[J]. Chinese Journal of Rock Mechanics and Engineering, 2013, 32(1): 41–48. |
[4] | Erarslan N, Williams D J. Mechanism of rock fatigue damage in terms of fracturing modes[J]. International Journal of Fatigue, 2012, 43: 76–89. DOI:10.1016/j.ijfatigue.2012.02.008 |
[5] |
王者超, 赵建纲, 李术才, 等. 循环荷载作用下花岗岩疲劳力学性质及其本构模型[J].
岩石力学与工程学报, 2012, 31(9): 1888–1899.
Wang Zhechao, Zhao Jiangang, Li Shucai, et al. Fatigue mechanical behavior of granite subjected to cyclic load and its constitutive model[J]. Chinese Journal of Rock Mechanics and Engineering, 2012, 31(9): 1888–1899. |
[6] |
朱珍德, 孙林柱, 王明洋. 不同频率循环荷载作用下岩石阻尼比试验与变形破坏机制细观分析[J].
岩土力学, 2010, 31(增1): 8–12.
Zhu Zhende, Sun Linzhu, Wang Mingyang. Damping ratio experiment and mesomechanical analysis of deformation failure mechanism on rock under different frequency cyclic loadings[J]. Rock and Soil Mechanics, 2010, 31(Supp.1): 8–12. |
[7] |
吴文, 杨春和, 侯正猛. 盐岩中能源(石油和天然气)地下储存力学问题研究现状及其发展[J].
岩石力学与工程学报, 2005, 24(增2): 5561–5568.
Wu Wen, Yang Chunhe, Hou Zhengmeng. Investigations on studied situations associated with mechanical aspects and development for underground storage of petroleum and natural gas in rocksalt[J]. Chinese Journal of Rock Mechanics and Engineering, 2005, 24(Supp.2): 5561–5568. |
[8] |
郭印同, 赵克烈, 孙冠华, 等. 周期荷载下盐岩的疲劳变形及损伤特性研究[J].
岩土力学, 2011, 32(5): 1353–1359.
Guo Yintong, Zhao Kelie, Sun Guanhua, et al. Experimental study of fatigue deformation and damage characteristics of salt rock under cyclic loading[J]. Rock and Soil Mechanics, 2011, 32(5): 1353–1359. |
[9] |
杨春和, 马洪岭, 刘建锋. 循环加、卸载下盐岩变形特性试验研究[J].
岩土力学, 2009, 30(12): 3562–3568.
Yang Chunhe, Ma Hongling, Liu Jianfeng. Study of deformation of rock salt under cycling loading and unloading[J]. Rock and Soil Mechanics, 2009, 30(12): 3562–3568. DOI:10.3969/j.issn.1000-7598.2009.12.002 |
[10] |
马林建, 刘新宇, 许宏发, 等. 循环荷载作用下盐岩三轴变形和强度特性试验研究[J].
岩石力学与工程学报, 2013, 32(4): 849–856.
Ma Linjian, Liu Xinyu, Xu Hongfa, et al. Deformation and strength properties of rock salt subjected to triaxial compression with cyclic loading[J]. Chinese Journal of Rock Mechanics and Engineering, 2013, 32(4): 849–856. |
[11] |
何满潮, 胡江春, 熊伟, 等. 岩石抗拉强度特性的劈裂试验分析[J].
矿业研究与开发, 2005, 25(2): 12–16.
He Manchao, Hu Jiangchun, Xiong Wei, et al. Splitting test and analysis of rock tensile strength[J]. Mining Research and Development, 2005, 25(2): 12–16. |
[12] |
中华人民共和国国家标准编写组. GB/T 23561-2010煤和岩石物理力学性质测定方法[S]. 北京: 中国标准出版社, 2010.
The National Standards Compilation Group of Peoples Republic of China. GB/T 23561-2010 Methods for Determining the Physical and Mechanical Properties of Coal and Rock[S]. Beijing: Standards Press of China, 2010. |
[13] | Muskhelishvilini. Some Basic Problems of the Mathematical Theory of Elasticity[M]. Groningen Holland: P.Noordhoff Ltd., 1953. |
[14] |
王启智, 贾学明. 用平台巴西圆盘试样确定脆性岩石的弹性模量、拉伸强度和断裂韧度——第一部分:解析和数值结果[J].
岩石力学与工程学报, 2002, 21(9): 1285–1289.
Wang Qizhi, Jia Xueming. Determination of elastic modulus, tensile strength and fracture toughness of brittle rocks by using flattened Brazilian disk specimen[J]. Chinese Journal of Rock Mechanics and Engineering, 2002, 21(9): 1285–1289. |
[15] |
尤明庆, 苏承东. 平台巴西圆盘劈裂和岩石抗拉强度的试验研究[J].
岩石力学与工程学报, 2004, 23(18): 3106–3112.
You Mingqing, Su Chengdong. Experimental study on split test with flattened disk and tensile strength of rock[J]. Chinese Journal of Rock Mechanics and Engineering, 2004, 23(18): 3106–3112. DOI:10.3321/j.issn:1000-6915.2004.18.014 |
[16] |
蒋宇, 葛修润, 任建喜. 岩石疲劳破坏过程中的变形规律及声发射特性[J].
岩石力学与工程学报, 2004, 23(11): 1810–1814.
Jiang Yu, Ge Xiurun, Ren Jianxi. Deformation rules and acoustic emission characteristics of rocks in process of fatigue failure[J]. Chinese Journal of Rock Mechanics and Engineering, 2004, 23(11): 1810–1814. DOI:10.3321/j.issn:1000-6915.2004.11.005 |
[17] |
郑达, 巨能攀. 千枚岩岩石微观破裂机理与断裂特征研究[J].
工程地质学报, 2011, 19(3): 317–322.
Zheng Da, Ju Nengpan. Scanning electronic microscope tests for rock micro-rupture mechanism and fracture characteristic of phyllite[J]. Journal of Engineering Geology, 2011, 19(3): 317–322. |